The purpose of a slabbing mill is to produce ‘slabs’ of steel which can then be processed into strip or plate steel.
Before the introduction of continuous casting at Ravenscraig, ingots of cold steel were brought to the slabbing mill, soaked in pits, reheated, run through the rolling mill and then cut using a 3,000 ton air-hydraulic slab shear.
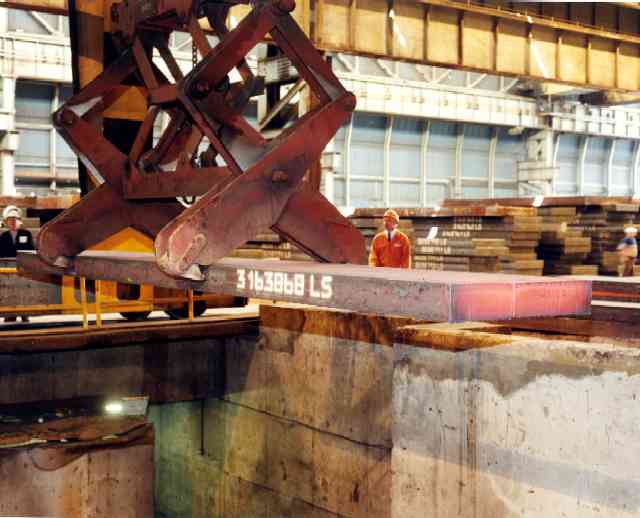
Last Slab Produced at Ravenscraig 1992 © Owens Ind & Comm Photographs
“Ravenscraig pioneered continuous casting in British Steel flat products…” Dr. Jeremy Bray (Motherwell, South) House of Commons, 21 May 1990. This was achieved by the introduction of two single-strand machines in 1974 and then with the addition of a third twin-strand machine in 1979.
The process involves a ladle of molten steel being carried to the casting plant by an overhead crane. The liquid is ‘stirred’ by the injection of inert gas and then placed onto a rotating turret. The steel is then poured into a reservoir called a tundish, a water cooled copper mould, which solidifies the outer shell of the liquid steel. The steel continues to curve downwards through a series of rollers until it completely emerges at the other end of the machine in an entirely solid state. The steel slabs are then cut to length by automatic gas-cutting equipment. When one ladle of steel is emptied into the machine another is moved into position to maintain a continuous flow via the tundish.
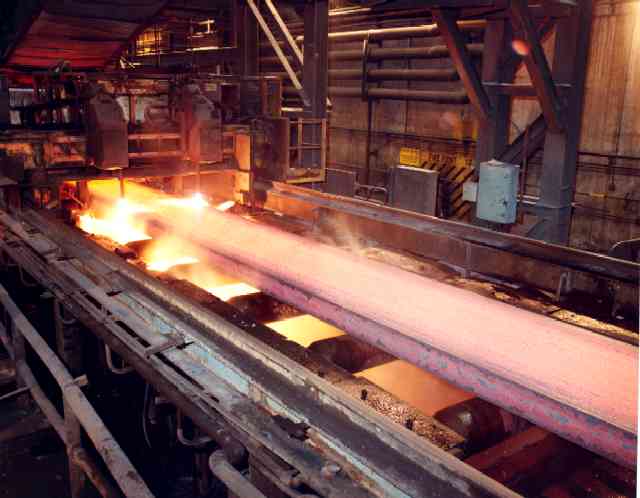
Continuous Casting Process
© Owens Ind & Comm Photographs