As a fully ‘integrated works’ Ravenscraig possessed the facilities to produce a finished product in-house from beginning to end. The Hot Strip Mill was a vital part of that process.
After having been scrutinised carefully at quality control, the steel slabs were sent to the hot strip mill where they were reheated to temperature then passed through the vertical and horizontal scale breakers. The oxide on the surface of the steel was broken and washed off using high-pressure water jets. The slabs then moved onto the completely automated 4-high Reversing Roughing Mill. The slabs moved back and forth a number of times reducing the thickness of the slab to around one inch and lengthening it to about 200ft. This then passed to the 6-stand 4-high Finishing Mill, where the metal was further reduced. By the time the steel reached the 6th stand it would be travelling at 31mph and have reached 4,000ft in length. The strip was then cooled with water sprays and coiled into the finished product.
The coils of strip metal were then sold on to customers requiring hot strip metal, unrolled and finished into light plate at the in-house temper mill or sent to the nearby Gartcosh Cold Reduction Mill.
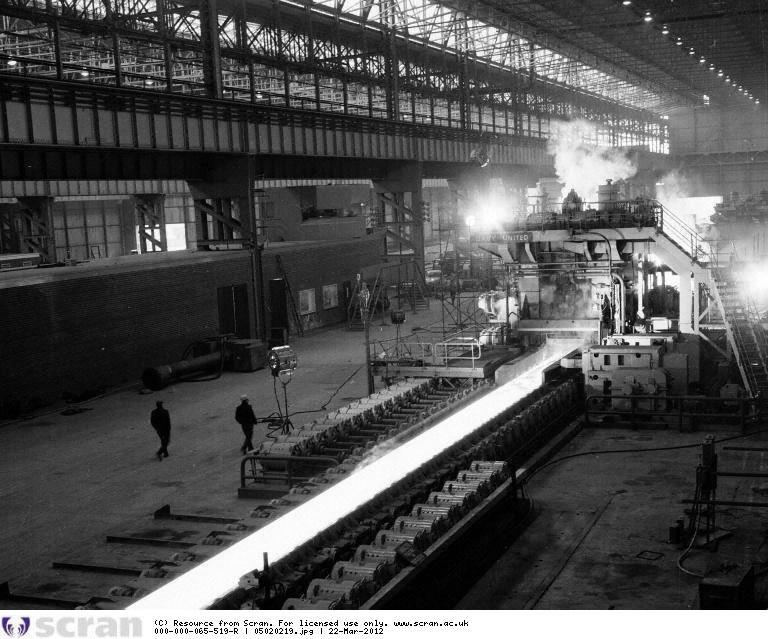
Lengths of steel pass through the rougher at the Strip Mill
© The Scotsman